Cooler boxes are essential for keeping food and drinks cold during outings, picnics, and camping trips. They come in various types, with injection-molded and rotomolded cooler boxes being two of the most popular options. Understanding the differences between these two types can help you choose the best cooler box for your needs. Let’s explore the differences between injection molding and rotomolding cooler boxes in detail.
What is Injection Molding?
Injection molding is a manufacturing process where melted plastic is injected into a mold. Once the plastic cools and hardens, it forms the desired shape. This method is commonly used to produce a wide range of plastic products, including cooler boxes.
Advantages of Injection Molding Cooler Boxes
- Cost-Effective: Injection molding allows for high-volume production, reducing the cost per unit. This makes injection-molded cooler boxes generally more affordable.
- Quick Production: The injection molding process is fast, allowing manufacturers to produce large quantities of cooler boxes in a short time.
- Precise Design: Injection molding provides high precision, resulting in cooler boxes with consistent shapes and sizes.
Disadvantages of Injection Molding Cooler Boxes
- Less Durable: Injection-molded cooler boxes are usually less durable compared to rotomolded ones. They might not withstand rough handling as well.
- Limited Insulation: The insulation in injection-molded cooler boxes is often not as efficient as that in rotomolded cooler boxes.
What is Rotomolding?
Rotomolding, or rotational molding, is a manufacturing process where plastic is placed in a mold that is then rotated slowly in an oven. The heat melts the plastic, which coats the inside of the mold. As the mold continues to rotate, the plastic forms a thick, even layer. Once cooled, the plastic retains the shape of the mold, creating a robust and durable product.
Advantages of Rotomolded Cooler Boxes
- High Durability: Rotomolded cooler boxes are incredibly tough and can withstand rough use and harsh conditions.
- Superior Insulation: The thick, uniform walls of rotomolded cooler boxes provide excellent insulation, keeping items cold for longer periods.
- Seamless Design: Rotomolded cooler boxes have a seamless construction, which reduces the risk of leaks and improves overall durability.
Disadvantages of Rotomolded Cooler Boxes
- Higher Cost: Due to the more complex manufacturing process, rotomolded cooler boxes are generally more expensive than injection-molded ones.
- Longer Production Time: The rotomolding process takes longer, resulting in slower production rates compared to injection molding.
Key Differences Between Injection Molding and Rotomolding Cooler Boxes
Understanding the differences between injection-molded and rotomolded cooler boxes can help you make an informed decision. Here are the key differences:
Manufacturing Process
- Injection Molding: Uses melted plastic injected into a mold, which then cools and hardens quickly. This process allows for high-volume, fast production.
- Rotomolding: Involves heating and rotating plastic inside a mold to form a thick, uniform layer. This process is slower but results in more durable products.
Durability
- Injection Molding: Cooler boxes made with this method are generally less durable and may not withstand heavy use as well as rotomolded cooler boxes.
- Rotomolding: Produces highly durable cooler boxes that can handle rough handling and extreme conditions.
Insulation
- Injection Molding: Often provides less effective insulation, meaning the cooler box may not keep items cold for as long.
- Rotomolding: Offers superior insulation due to the thick, uniform walls, keeping items cold for extended periods.
Cost
- Injection Molding: Generally results in more affordable cooler boxes due to the lower production costs.
- Rotomolding: Cooler boxes are usually more expensive because of the complex and time-consuming manufacturing process.
Design and Features
- Injection Molding: Allows for precise designs and features, making it possible to produce cooler boxes with consistent shapes and sizes.
- Rotomolding: While it may not offer the same level of precision, it provides a seamless design that enhances durability and insulation.
Choosing the Right Cooler Box
When deciding between an injection-molded and a rotomolded cooler box, consider your specific needs and preferences. Here are some factors to keep in mind:
Budget
If you are on a tight budget, an injection-molded cooler box might be the better choice. These cooler boxes are typically more affordable and still provide adequate performance for most casual uses.
Durability
For those who need a cooler box that can withstand rough handling and harsh conditions, a rotomolded cooler box is the way to go. Its high durability ensures it will last longer, even with frequent use.
Insulation
If keeping items cold for extended periods is a priority, a rotomolded cooler box offers superior insulation. This is particularly important for long camping trips or outdoor activities where access to ice or refrigeration is limited.
Weight and Portability
Consider the weight and portability of the cooler box. Injection-molded cooler boxes are often lighter and easier to carry, making them ideal for short trips or when you need to move the cooler frequently. Rotomolded cooler boxes, while heavier, offer better durability and insulation.
Design and Features
Think about the design and additional features you may need. Injection-molded cooler boxes can come with various built-in features, such as cup holders or compartments, providing added convenience. Rotomolded cooler boxes may have fewer features but compensate with their robust build and excellent insulation.
Conclusion
Both injection-molded and rotomolded cooler boxes have their unique advantages and disadvantages. Injection molding offers cost-effective, quick production and precise design but falls short in durability and insulation. Rotomolding provides superior durability and insulation but comes at a higher cost and longer production time.
Choosing the right cooler box depends on your needs and preferences. Consider your budget, the importance of durability and insulation, weight and portability, and any specific design features you may require. By understanding the differences between these two types of cooler boxes, you can make an informed decision and select the perfect cooler box for your outdoor adventures.
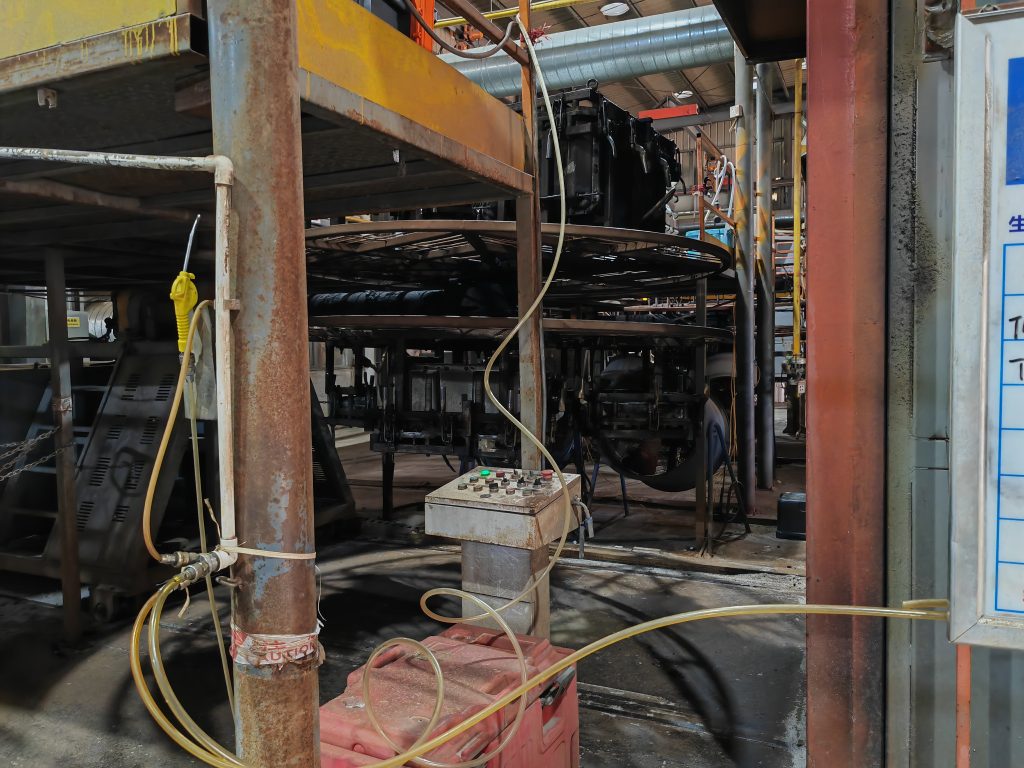