Differences Between Blow Molded and Rotomolded Insulated Boxes
In the realm of insulated boxes, two prominent manufacturing techniques stand out: blow molding and rotomolding (also known as rotational molding). Both processes are employed to create containers designed for thermal insulation, commonly used in various industries for transporting temperature-sensitive goods. While these methods share a common goal of producing insulated containers, they differ significantly in their approaches, resulting in distinct characteristics that cater to diverse needs and preferences. In this article, we delve into the disparities between blow molded and rotomolded insulated boxes across multiple dimensions, including their applications, manufacturing processes, materials, costs, and prices.
Applications:
Blow Molded Insulated Boxes:
Blow molded insulated boxes are widely utilized in industries such as food and beverage, pharmaceuticals, and logistics. These boxes are favored for applications requiring lightweight yet durable containers with moderate insulation properties. They are commonly used for short to medium-term storage and transportation of perishable goods, pharmaceuticals, and medical supplies.
Rotomolded Insulated Boxes:
Rotomolded insulated boxes find extensive applications in industries where durability and superior insulation are paramount. These boxes are ideal for long-term storage and transportation of goods that require stringent temperature control, such as frozen foods, vaccines, chemicals, and scientific samples. They are also favored for outdoor activities like camping and fishing due to their rugged construction.
Manufacturing Process:
Blow Molded Insulated Boxes:
The blow molding process involves melting plastic resin and shaping it by forcing air into a hollow mold cavity. This process results in a seamless, lightweight container with uniform wall thickness. In the case of insulated boxes, a layer of insulating material such as foam is injected into the cavity during the blow molding process, providing thermal insulation.
Rotomolded Insulated Boxes:
Rotomolding, on the other hand, entails placing a measured amount of plastic resin powder into a hollow mold, which is then heated and rotated bi-axially. The rotation ensures even distribution of the melted resin, resulting in a hollow, uniform wall thickness. Once cooled, the mold is opened to reveal the finished product. Insulated versions incorporate an inner and outer shell with a layer of insulating material sandwiched between them, providing excellent thermal insulation properties.
Materials:
Blow Molded Insulated Boxes:
Blow molded insulated boxes are typically made from high-density polyethylene (HDPE) or polypropylene (PP) due to their favorable properties, including durability, resistance to chemicals, and ease of processing. The insulating layer may consist of expanded polystyrene (EPS) foam or polyurethane foam, depending on the desired insulation performance.
Rotomolded Insulated Boxes:
Rotomolded insulated boxes are also predominantly crafted from HDPE or other suitable polymers known for their robustness and resistance to impact and environmental factors. The insulation layer often comprises foam materials like polyurethane (PU) or polyethylene foam, offering superior thermal insulation properties compared to blow molded counterparts.
Costs and Prices:
Blow Molded Insulated Boxes:
Due to the simpler manufacturing process and lower material costs, blow molded insulated boxes generally have a lower production cost compared to rotomolded counterparts. Consequently, these boxes are often more affordable for businesses and consumers. However, the price can vary depending on factors such as size, insulation thickness, and customization options.
Rotomolded Insulated Boxes:
Rotomolded insulated boxes tend to have higher production costs due to the complexity of the manufacturing process, longer production times, and the use of premium materials. As a result, they are usually priced higher than blow molded alternatives. Despite the higher upfront cost, their durability and superior insulation properties often justify the investment, particularly for applications requiring long-term reliability and performance.
Conclusion:
In summary, both blow molded and rotomolded insulated boxes offer unique advantages and cater to different requirements across various industries. While blow molded boxes excel in lightweight construction and affordability, rotomolded boxes boast superior durability and insulation capabilities, making them suitable for demanding applications where maintaining precise temperature conditions is critical. Understanding the distinctions between these two manufacturing processes is essential for businesses and consumers alike to make informed decisions based on their specific needs and priorities.
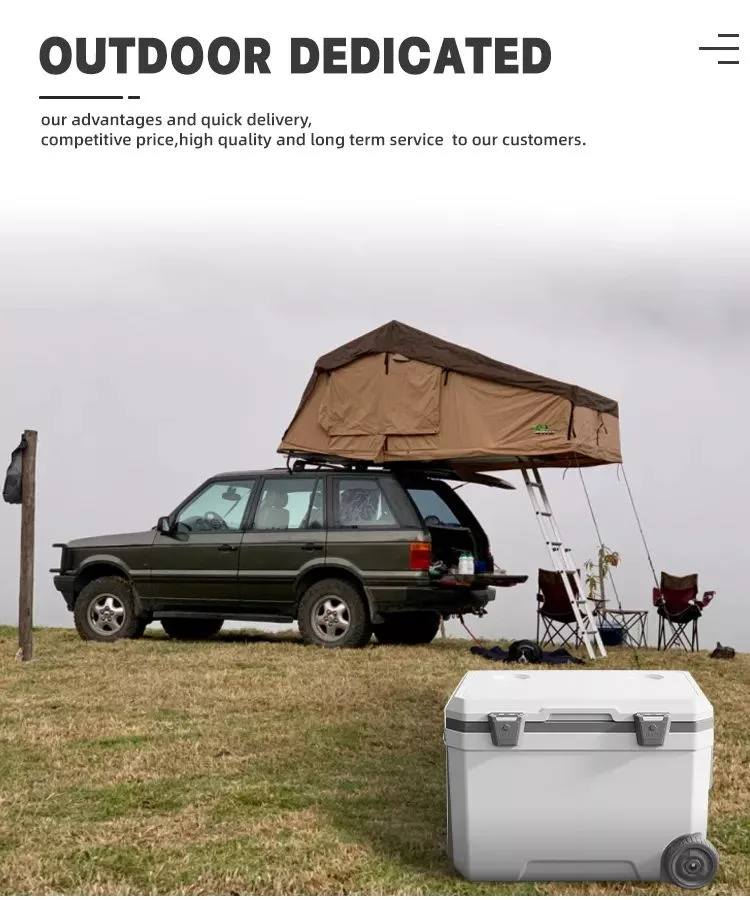