roto molding Kayak
1. Production Technology
Roto molding kayak
also known as rotational molding, rotational molding or rotary molding, is a hollow molding method for thermoplastics. The method is to add plastic raw materials into the mold first, then the mold is continuously rotated along two vertical axes and heated, and the plastic raw materials in the mold are gradually and uniformly coated and melted and adhered to the mold cavity under the action of gravity and heat. On the entire surface, it is formed into the desired shape, and then cooled and shaped to form a product.
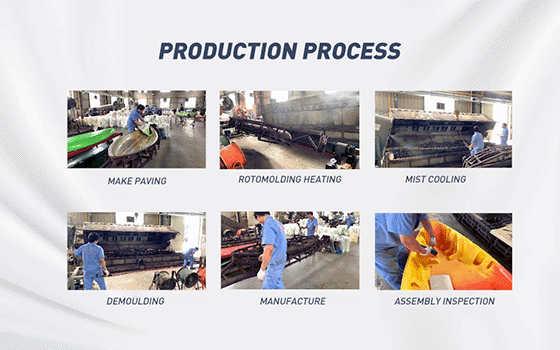
Blow molding kayak
Also known as hollow blow molding, is a rapidly developing plastic processing method. The tubular plastic blank obtained after thermoplastic resin extrusion or injection is put into the split mold while it is hot (or heated to a softened state). Immediately after the mold is closed, the compressed air is passed into the mold blank, so that the plastic blank expands and closes to the inner wall of the mold, and various hollow products are obtained after cooling and demoulding.
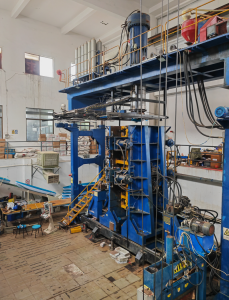
Thermoforming kayak
A kind of plastic processing technology, the main principle is to heat and soften the flat hard plastic sheet, then absorb it on the surface of the mold by vacuum, and form it after cooling. It is widely used in plastic packaging, lighting, advertising, decoration and other industries.
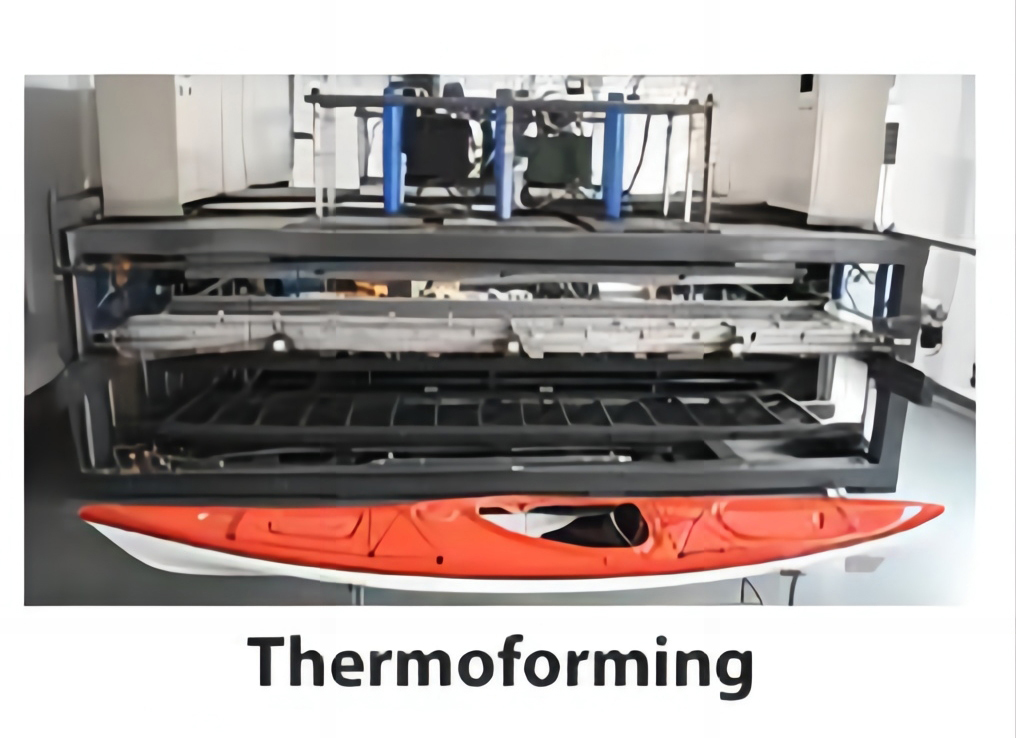
2. Cost
Thermoforming kayak > Rotational molding kayak > Blow molding kayak
Roto molding kayak
The mold price is relatively cheap, and the product price is relatively high. It mainly produces hollow products, packaging products and super-large products. The shrinkage ratio is relatively large and the output is relatively low. Rotational molding products are relatively large. Plastic particles are put into the mold to heat, and then the mold is continuously rolled to make the plastic adhere to the inner wall of the mold.
Blow molding kayak
The cost of the mold is lower than that of the mold, and it is relatively simple. The production cost of the article is also lower.
Thermoforming kayak
Lightest material – ABS and glued hull manually
3. Production Capacity
Blow molding kayak > Rotational molding kayak > Thermoformingkayak
Blow molding – 150-200 PCS/Machine/day
Roto molding – 15-20 PCS/Machine/day
Thermoforming molding – 5-10 PCS/day
4. Advantage For Different Kayaks
Blow molding kayak
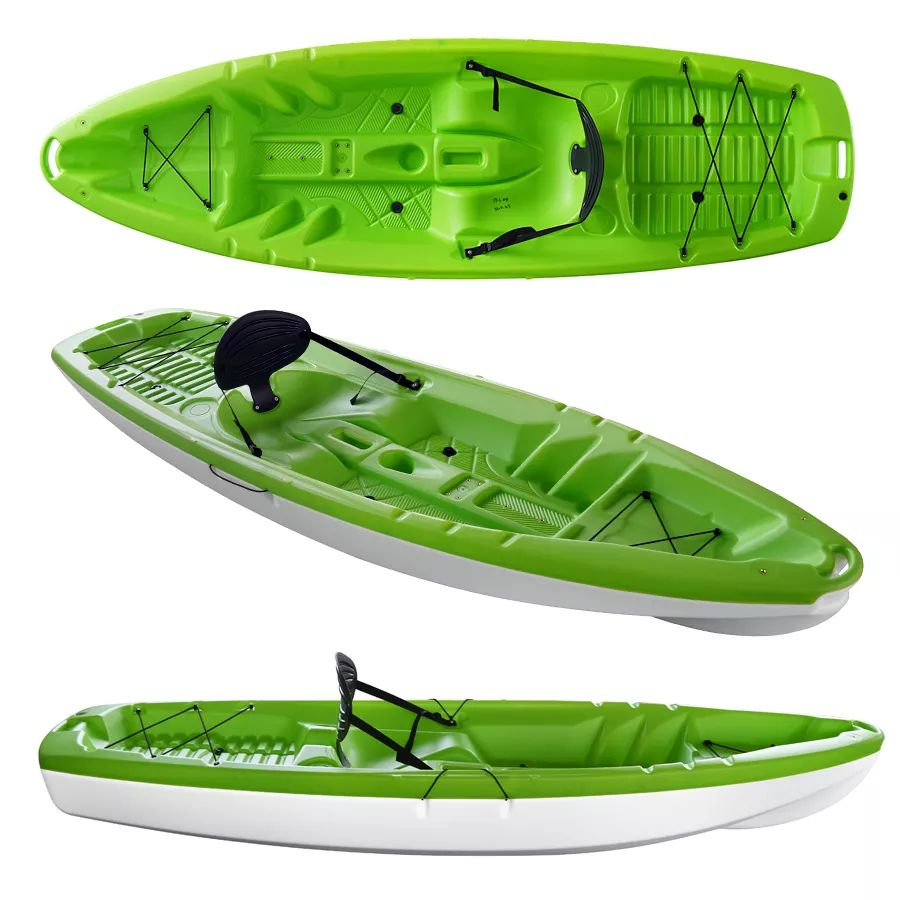
- Lower Cost
- High production capacity
- High strength and hardness,
- High creep resistance, gloss and moisture permeability resistance,
- Good oil, grease, acid and alkali resistance, and widely used in a wide range of applications.
Rotational molding kayak
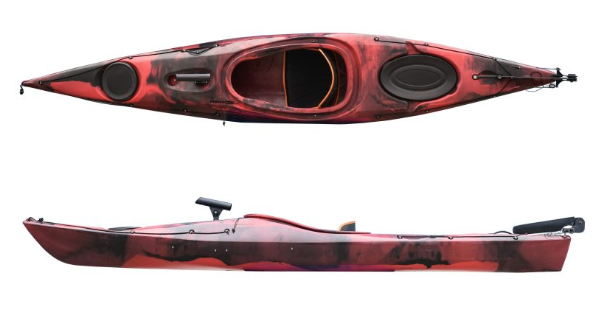
- Good flexibility and ductility,
- strong pressure resistance.
- Durable and hard
Thermoforming molding kayak
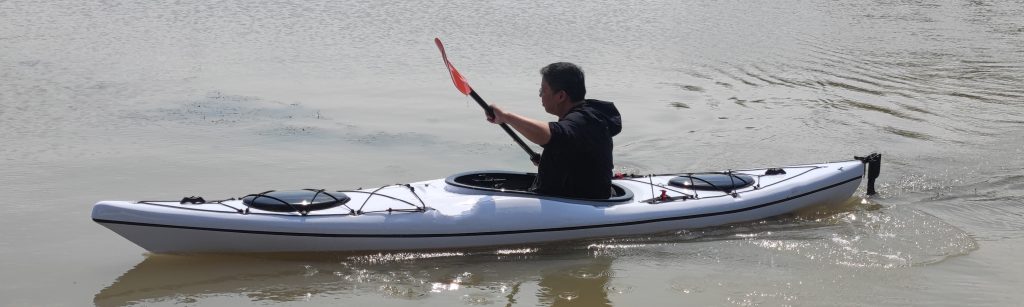
- Lighter Hull
- Faster experience
- Easy Carrying
- High impact resistance
What is a Roto Molding Kayak?
A roto molding kayak is made using a manufacturing process called rotational molding. This process involves heating powdered plastic inside a mold while it rotates. The melted plastic evenly coats the interior of the mold, creating a hollow, seamless kayak. This method results in a robust and uniform product, ideal for outdoor activities.
Benefits of Roto Molding Kayaks
- Durability
Roto-molded kayaks are known for their toughness. The seamless construction makes them resistant to impacts, scratches, and cracks. Whether you’re paddling in rocky rivers or rugged coastlines, a roto-molded kayak can handle the challenge. - Affordability
The production process of rotational molding is cost-efficient. This translates to lower prices for consumers, making these kayaks a great choice for beginners and experienced paddlers alike. - Design Flexibility
Roto molding allows manufacturers to create kayaks in various shapes, sizes, and colors. This means you can find models designed for fishing, touring, or recreational use, all crafted to meet specific needs. - Low Maintenance
With their rugged design and material, roto-molded kayaks require minimal upkeep. A simple rinse after use and occasional cleaning is often enough to keep them in good condition.
Why Choose a Roto Molding Kayak?
Roto-molded kayaks are versatile and suitable for all types of paddlers. Here’s why you should consider them:
- Beginners: These kayaks are user-friendly and forgiving, making them ideal for first-time paddlers.
- Adventurers: Their durability makes them perfect for challenging environments like whitewater rivers or open seas.
- Anglers: Specialized roto-molded fishing kayaks come equipped with features like rod holders and storage compartments.
Key Features of Roto Molding Kayaks
- Seamless Construction
The lack of seams ensures better durability and water resistance. - Material
Most roto-molded kayaks are made from high-density polyethylene (HDPE), a material that is lightweight yet strong. - Customizable Add-Ons
Many kayaks come with optional features such as padded seats, footrests, and gear storage compartments.
Popular Types of Roto Molding Kayaks
- Recreational Kayaks: Lightweight and easy to maneuver, perfect for calm waters.
- Fishing Kayaks: Built with stability and equipped with angler-friendly features.
- Touring Kayaks: Designed for long-distance paddling, offering comfort and efficiency.
Final Thoughts
A roto molding kayak is a fantastic investment for anyone passionate about water adventures. Its durability, affordability, and versatility make it a top choice among paddlers. Whether you’re a beginner or a seasoned kayaker, there’s a roto-molded kayak that’s perfect for your needs.
So, if you’re ready to embark on your next water adventure, consider a roto molding kayak.